OEM Die Casting Parts
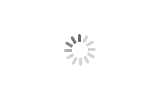
- SHD Precision Tech
- Shenzhen
- 2 Weeks
- depends on the product
Variable wall thicknesses
Tighter tolerances
Fewer steps from raw material to finished part
Fast production cycle times
Reduction in material scrap
Long tool life, especially for zinc and magnesium
Main Parameter:
Product Type | Die Casting Service | |||
Materials | Aluminum alloy, zinc alloy, magnesium alloy, brass and etc. | |||
Surface Treatment | Anodizing, Brushing, Galvanized, Laser engraving, Silk printing, Polishing, Powder coating, and etc. | |||
Tolerance | ±0.01mm, 100% QC quality inspection before delivery, provide quality inspection form; | |||
Testing equipment | CMM; Tool microscope; Multi-joint arm; Automatic height gauge; Manual height gauge; Dial gauge ; Marble platform; Roughness measurement. | |||
File Formats | STP/ STEP/AutoCAD(DXF,DWG),PDF,TIF etc. |
Types of Die Casting Processes
The two die casting processes used industrially are hot chamber, and cold chamber dies casting. Each one has its peculiarities and is applicable in different scenarios. Below are what the two types of processes entail.
Hot Chamber Die Casting
The hot chamber die casting process is the perfect method for working with low melting point materials such as zinc, tin, lead, and magnesium alloys. It is not suitable for alloys with a higher melting point as it would damage the pump as the pump would directly contact the metal. It involves melting the metal and injecting it into the die using pressure from a hydraulic system.
Cold Chamber Die Casting
The cold chamber die casting is the perfect method for working with high melting point materials such as aluminum. This process is ideal for such metals as the high temperature needed to melt the material can damage the pumping system.
The process involves ladling the melted material into a cold chamber before injection into the die. The hydraulic system used in a cold chamber process is similar to that of the hot chamber process. However, it might require a larger pressure ranging from 2000 to 20000 psi.
Advantages Of DIE CASTING
Die casted parts are strong, made of solid metal
Metal parts can be produced in complex dimensions
One mould produces thousands of identical casts
Complex mathematical accuracy
Brilliant surface finishes available
Heat, chemical, and pressure resistant
Efficient and repeatable manufacturing process
Fastest method for creating metal parts in volume