Compound Die Casting Parts Aluminium Alloy
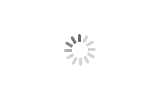
- SHD Precision Tech
- Shenzhen
- 2 Weeks
- depends on the product
Variable wall thicknesses
Tighter tolerances
Fewer steps from raw material to finished part
Fast production cycle times
Reduction in material scrap
Long tool life, especially for zinc and magnesium
Main Parameter:
Product Type | Die Casting Service | |||
Materials | Aluminum alloy, zinc alloy, magnesium alloy, brass and etc. | |||
Surface Treatment | Anodizing, Brushing, Galvanized, Laser engraving, Silk printing, Polishing, Powder coating, and etc. | |||
Tolerance | ±0.01mm, 100% QC quality inspection before delivery, provide quality inspection form; | |||
Testing equipment | CMM; Tool microscope; Multi-joint arm; Automatic height gauge; Manual height gauge; Dial gauge ; Marble platform; Roughness measurement. | |||
File Formats | STP/ STEP/AutoCAD(DXF,DWG),PDF,TIF etc. |
Die Casting Alloys
Most alloys used in die casting are non-ferrous with strong mechanical properties. The non-ferrous moiety is responsible for the low melting point in agreement with the strong mechanical properties. The type of properties needed depends on the material being worked on. Consequently, there is no limitation when choosing a material. However, below are several popular alloys:
Aluminum Alloys
Aluminum alloys have unique properties, making them applicable in making a wide range of products. On the one hand, aluminum alloy 380.0 is the most common material in die casting due to its unique properties. Other alloys include Aluminum Alloys 360, 390, and 413. You can use aluminum alloys because of the following:
High operating temperatures
Outstanding corrosion resistance
Lightweight
Very good strength and hardness
Good stiffness and strength-to-weight ratio
Excellent EMI and RFI shielding properties
Excellent thermal conductivity
High electrical conductivity
Good finishing characteristics
Full recyclability
Withstand the highest operating temperatures of all the diecast alloys
Corrosion-resistance
It retains high dimensional stability with thin walls
Zinc Alloys
Zinc alloys have incredible strength, toughness, firmness, performance, and cost-effectiveness. As a result, they are an important part of the die casting process, with properties rivaling and exceeding other alloys such as aluminum, magnesium, and bronze.
There are many alloys of zinc you can use. However, the common die casting zinc materials are Zamak #2, #3, #5, #7, ZA8 and ZA27, known for the following properties:
Improved Castability
Shortened Cycle Time
Extended Die Life
Ideal Mechanical Qualities
Magnesium Alloys
Magnesium is another material used for die casting. It has many alloys, but the most common one is the AZ91D, known for its toughness, durability, lightweight and good castability. It is 75% lighter than steel and 33% lighter than aluminum without a loss in strength. Most enthusiasts prefer magnesium as it is better for complex casting with tight tolerances and it has better corrosion resistance.
Other Alloys
Other alloys suitable for making die casting parts include Bronze, Brass, lead, and tin.
Tin is the first material used in die casting due to its high fluidity. It has a low melting point, and it leaves little or no wear on the molds.
Bronze (white bronze) is the right die cast material used in the jewelry industry. It has a similar color to white gold and stainless steel alloys but is suitable for die casting due to its low melting point.