Die Casting Parts For Automotive
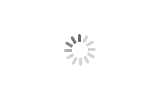
- SHD Precision Tech
- Shenzhen
- 2 Weeks
- depends on the product
Variable wall thicknesses
Tighter tolerances
Fewer steps from raw material to finished part
Fast production cycle times
Reduction in material scrap
Long tool life, especially for zinc and magnesium
Main Parameter:
Product Type | Die Casting Service | |||
Materials | Aluminum alloy, zinc alloy, magnesium alloy, brass and etc. | |||
Surface Treatment | Anodizing, Brushing, Galvanized, Laser engraving, Silk printing, Polishing, Powder coating, and etc. | |||
Tolerance | ±0.01mm, 100% QC quality inspection before delivery, provide quality inspection form; | |||
Testing equipment | CMM; Tool microscope; Multi-joint arm; Automatic height gauge; Manual height gauge; Dial gauge ; Marble platform; Roughness measurement. | |||
File Formats | STP/ STEP/AutoCAD(DXF,DWG),PDF,TIF etc. |
Steps of Die Casting Process
Whether hot or cold chamber die casting, the standard process involves injecting molten metal into a die mold under high pressure. Below are the intricate die casting process steps:
Clamping
The first step in die casting is clamping. However, before then, clean the die to remove any impurities and lubricate the die for better injection and removal of the solidified product. After cleaning and lubrication, clamp and close the die with high pressure.
Injection
Melt the metal you want to inject and pour it into the shot chamber. The procedure depends on the process you are using. For example, the shot chamber is cold in the cold chamber die casting, while it is hot in the hot chamber die casting. After that, inject the metal into the die under high pressure generated by a hydraulic system.
Cooling
While clamped, allow the metal to cool for solidification. The solidified material will have a shape similar to the design of the mold.
Ejection
After unclamping the die mold, an ejection mechanism will push the solid casting out of the die. Ensure proper solidification before ejecting the final product.
Trimming
This is the final step, and it involves the removal of the excess metal in the sprue and runner found on the finished product. Trimming is achievable using a trim die, saw, or other procedures. The removed metal parts are recyclable and reusable in the process.