Metal Compound Die Casting Parts
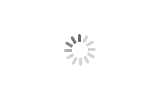
- SHD Precision Tech
- Shenzhen
- 2 Weeks
- 5000 pcs / month
Variable wall thicknesses
Tighter tolerances
Fewer steps from raw material to finished part
Fast production cycle times
Reduction in material scrap
Long tool life, especially for zinc and magnesium
Main Parameter:
Product Type | Die Casting Service | |||
Materials | Aluminum alloy, zinc alloy, magnesium alloy, brass and etc. | |||
Surface Treatment | Anodizing, Brushing, Galvanized, Laser engraving, Silk printing, Polishing, Powder coating, and etc. | |||
Tolerance | ±0.01mm, 100% QC quality inspection before delivery, provide quality inspection form; | |||
Testing equipment | CMM; Tool microscope; Multi-joint arm; Automatic height gauge; Manual height gauge; Dial gauge ; Marble platform; Roughness measurement. | |||
File Formats | STP/ STEP/AutoCAD(DXF,DWG),PDF,TIF etc. |
History of Die Casting in Manufacturing
Die casting dates as far back as 1800 and was an important technique in the printing industry. In 1849, Sturges made the hand manually operated die casting machine used in printing, making it more accurate, creative, and persistent when making different complex shapes. Later in 1855, Otto Mergenthaler made the linotype machine known for its better efficiency and is an important part of the publishing industry.
The demand for die casting machines grew in the 19th century due to their advantages. Consequently, die casting became popular in many industries. During this period, there was technological advancement. For example, aluminum replaced tin and lead due to their higher quality. Also, the original process of low-pressure injection die casting changed to high-pressure casting methods.
Advantages Of DIE CASTING
Die casted parts are strong, made of solid metal
Metal parts can be produced in complex dimensions
One mould produces thousands of identical casts
Complex mathematical accuracy
Brilliant surface finishes available
Heat, chemical, and pressure resistant
Efficient and repeatable manufacturing process
Fastest method for creating metal parts in volume