Customized Vacuum Casting Parts
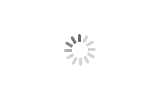
- SHD Precision Tech
- Shenzhen
- 1 week
- 5000 pcs / month
Low cost for silicone molds
Fast delivery
A wide selection of materials
High precision and fine details
Excellent surface finish
Main Parameter:
Mold Base Materials | P20/718/738/NAK80/S136 and others |
Cavity | Single/ Multi |
Runner | Hot / Cold |
Mold Life/Usage | 300,000~1,000,000 shots |
Plastic Materials | ABS, PC, PMMA, PP, PBT, PE, Nylon and others |
Design software | UG, Pro-E, Solid works, Auto CAD and others |
Tolerance | 0.01mm |
How Vacuum Casting Works
The vacuum casting process has three steps: master pattern, molding, and casting.
Step 3. Casting Process
SHD Precision Tech standardized operational procedures assure accurate part replication and consistent mechanical properties. Our vacuum casting technicians to control all operational parameters: mixing, de-gassing, stirring, preheating, casting, and de-molding, allowing for near-perfect copies of the master pattern to be created. The manufacturing processes of vacuum casting parts are as follows:
First, put the silicone mold into the oven and preheat it to 60-70°C.
It is very important to choose a suitable release agent before closing the mold and use it correctly to avoid stickiness and surface defects.
Prepare the polyurethane resins to preheat them to about 40°C before use. Mix two-component casting resins in exact proportions, and then fully stir and degas for 50-60 seconds under vacuum to avoid air pockets or bubbles
The resin is poured into the mold inside the vacuum chamber under computer control and cured again in the oven. Average cure time: 1-3 hours for small parts and 3-6 hours for big parts.
Remove the casting part from the silicone mold after curing. Prepare to repeat this vacuum casting work cycle.